派利文库
派利文库
精益生产:“精益布局”解析
更新日期:2015-01-13 阅读:2945 次
随着原材料价格及工资的大幅上升,环保成本的增加,人民币的快速升值,电荒、用工荒、融资荒以及全球经济格局的调整,企业已经明显感觉到“严冬”寒气逼人。同质化时代背景下的竞争,价格仍是顾客选择产品或服务的重要指标之一。如何节约企业运营成本?很多企业尝试推行“精益生产”,但相当一部分企业并未获得成功,甚至带来了负面影响(据有关资料统计约1/3的企业效果不理想或有负面效应)。究其原因,问题的核心是这些企业没有全面掌握精益生产的体系架构、方法及工具。精益生产的推行只停留在5S,标准化等一些局部模块的改善,并未进行系统的优化及改善,可谓“管中窥豹,只见一斑”。派利顾问公司认为,系统性、个性化的采取精益生产方法,成为精益企业的战略选择。
案例:笔者前不久在一家专业运动器材生产企业调研时了解到,该企业多年来沿用传统的生产方式,今年初以来,客户每次所下订单批量仅为过去的1/10,为典型的小批量多品种。面对严峻的市场环境,该企业总经理觉得,必须采取有异于常规的生产方式。经过与派利顾问进行多次接触后,决定在企业导入精益生产方式。笔者随后在深入现场后了解到,该企业的生产车间为传统的功能式布局(详见简图<二>),存在如下问题:
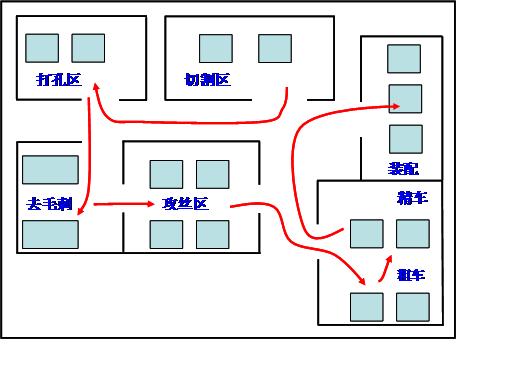
模型简图<二>
布局不合理——设备布局未实现流线化,搬运路线长,导致大量的搬运浪费;
产品库存多——大批量生产,工序间存在大量的在制品库存;
生产能力不均衡——各工序“独立作战”,工序间忙闲不均,存在大量的等待浪费;
生产周期长——工序间大量的在制品,致使经常无法满足客户的交期需求;
厂房面积利用率低——厂房面积利用率仅为65%。
……
通过与该企业管理人员的沟通了解到,大部分管理人员把这些问题归咎为订单单量太小、场地太小、设备老化,人手不足。管理人员当时的做法,只是不断地向公司高层反映这类问题。针对这种情况, 笔者认为,实施“精益布局”才是王道!孙子兵法云:“善阵者不战”,可见排兵布阵之重要性,其实在企业经营管理中,亦有异曲同工之处,精益的布局可将企业诸多的浪费扼杀在摇篮里,如果将一个工厂的浪费看做100%的话,那么实施精益布局就可以消除60%~70%的浪费,且实施精益布局所花费的成本较少,因此精益布局可以说是精益生产体系的一个重要的方法和工具。
什么是精益布局呢?所谓精益布局就是研究车间之间、工序之间以及工厂整体的设备、工作台、原材料、成品仓库等配置的合理性,通过消除人、机、料、法、环各个环节上的浪费,来实现生产要素最佳组合的生产方式,以达到整个生产系统的流程最优化、人流、物流畅通化、搬运最小化、效率最大化的目标。
实施精益布局可以帮助该企业解决哪些问题?首先,可以最大限度地减少移动及搬运距离等,增加作业的附加价值;第二,可以实现流线化生产,减少在制品库存,从而缩短生产周期;第三,可以大幅提高工序间的平衡,减少等待浪费,提升生产效率;第四,可以提高空间利用率及单位面积利用率;第五,还可以提升产品品质,改善作业环境。
企业到底应该如何实施精益布局?同样以上述企业的精益布局咨询项目为例,分享如下观点:
首先需要进行精益生产意识的塑造。对公司的各级员工,进行相关的精益生产的教育训练,塑造精益生产的氛围,然后选定以机械加工线为改善试点线,建立改善的信心,在试点线改善完成后进一步在全厂展开推广。
在具体的改善过程中,首先依据客户的需求,计算出节拍时间,再测定每个工序的加工时间及人力时间,根据这些数据的分析结果,考虑生产线的平衡,决定设立三条生产线。每一条生产线所需要的机器设备数量掌握清楚之后,实施精益布局,将机器设备按照产品工艺顺序布置(详见简图<三>),舍弃了改善前的大批量生产方式,将批量的传输方式改为做一个,检查一个,立即传到下一制程的“单件流动”生产方式,以减少工序间的在制品库存,因为剔除了产品在工序间的等待时间,进而使得整个生产周期大幅缩短,此外改变了作业人员的配置方式,舍弃固定的一人一个工序的“单能工”配置方式,而改用以节拍时间为基础来决定人员的配置,并且采用多能工作业方式。
通过改善,使生产周期由改善前的11天缩短至4天,生产效率由原来的每人每天生产150件提升到280件,产品的返修率也从原来的17%下降至7%,厂地面积由改善前的1560平方米缩减至980平方米,改善后有形绩效为:年节省金额102万元RMB;在无形绩效方面,公司的精益生产氛围整体得到提升,物流通道畅通化、透明化,生产现场的异常状况更加容易识别,现场的工作环境也因在制品库存的减少显得更加开阔明亮,井然有序,员工也能发挥互助合作的团队精神。
1. 统一原则:在精益布局设计和改善时,必须将各工序的人、机、料、法、环5要素有机结合起来并保持充分的平衡,因为5要素一旦没有统一协调好,作业容易割裂,增加物料搬运的次数等浪费。
2. 最短距离原则:在精益布局设计与改善时,必须要遵循移动距离,移动时间最小化,因为移动距离越短,物料搬运所浪费的时间和费用就越小。
3. 人流物流畅通原则:在进行精益布局时,必须使工序没有堵塞,物流顺畅无阻。在精益布局时应特别注意:尽量避免倒流交叉现象,否则会导致一系列意想不到的后果,如品质问题、管理难度问题、生产效率问题、安全问题等。
4. 充分利用立体空间原则:随着地价的不断攀升,企业厂房投资也水涨船高,因此如何充分利用立体空间就变得尤其重要,它直接影响到产品直接成本的高低。
5. 灵活机动原则:应尽可能适应变化、随机应变、如面对工序的增减、产能的增减能灵活应对。为了能达成灵活机动原则,在设计时需要将线、电、气与作业台分离、不要连成一体、设备尽量不要落地生根而采取方便移动的装置。
6. 安全满意原则:在进行精益布局设计时,必须确保作业人员的作业即安全又轻松,因为,只有这样才能减轻作业疲劳。请切记:材料的移动、旋转动作等可能会产生安全事故,抬升、卸下货物动作等也可能会产生安全事故,同时也会加剧作业的疲劳度。
精益布局是一个不断改进,不断完善的过程,需要不断执行PDCA改善,切记:“布局是没有最好,只有更好!
企业推动精益布局的过程,不是简单的设备、工装的搬迁,需要各个部门人员的协同合作和支持,这是一个系统工程,特别需要企业高层领导的支持和长远的视野。采用精益布局,也会由于一系列的原因导致产能的波动,我们需要坚定信心,实现我们既定的目标,这样才会在精益之路上走得更远。
作者简介:
王海军,现任深圳市派利企业管理顾问有限公司管理顾问。曾任世界500强富士康科技集团CMMSG事业群IE主管、专案Leader、CMMSG事业群精益变革小组核心成员,在现场管理方面拥有丰富的实战经验,对精益生产有着全面的视野和独到的见解。专长领域:精益生产、现场管理。
(图一:派利顾问公司精益生产管理体系示意图)
派利顾问公司的精益生产体系(见图<一>)以5S及目视化、持续改善为基础,以准时化、自働化为支柱,以价值流、精益布局、标准作业、工作研究、产线平衡、OEE(全局设备效率)、TPM(全员生产维护)、SMED(快速换型)、看板管理、一个流、单元生产12个模块组成的智能大厦,它是一项系统管理体系,它追求生产系统整体优化,所以企业在推动精益生产的过程中需要结合实际情况选择适当的精益模块,并注重精益生产的综合性与整体性,才能取得良好的整体效果。案例:笔者前不久在一家专业运动器材生产企业调研时了解到,该企业多年来沿用传统的生产方式,今年初以来,客户每次所下订单批量仅为过去的1/10,为典型的小批量多品种。面对严峻的市场环境,该企业总经理觉得,必须采取有异于常规的生产方式。经过与派利顾问进行多次接触后,决定在企业导入精益生产方式。笔者随后在深入现场后了解到,该企业的生产车间为传统的功能式布局(详见简图<二>),存在如下问题:
模型简图<二>
产品库存多——大批量生产,工序间存在大量的在制品库存;
生产能力不均衡——各工序“独立作战”,工序间忙闲不均,存在大量的等待浪费;
生产周期长——工序间大量的在制品,致使经常无法满足客户的交期需求;
厂房面积利用率低——厂房面积利用率仅为65%。
……
通过与该企业管理人员的沟通了解到,大部分管理人员把这些问题归咎为订单单量太小、场地太小、设备老化,人手不足。管理人员当时的做法,只是不断地向公司高层反映这类问题。针对这种情况, 笔者认为,实施“精益布局”才是王道!孙子兵法云:“善阵者不战”,可见排兵布阵之重要性,其实在企业经营管理中,亦有异曲同工之处,精益的布局可将企业诸多的浪费扼杀在摇篮里,如果将一个工厂的浪费看做100%的话,那么实施精益布局就可以消除60%~70%的浪费,且实施精益布局所花费的成本较少,因此精益布局可以说是精益生产体系的一个重要的方法和工具。
什么是精益布局呢?所谓精益布局就是研究车间之间、工序之间以及工厂整体的设备、工作台、原材料、成品仓库等配置的合理性,通过消除人、机、料、法、环各个环节上的浪费,来实现生产要素最佳组合的生产方式,以达到整个生产系统的流程最优化、人流、物流畅通化、搬运最小化、效率最大化的目标。
实施精益布局可以帮助该企业解决哪些问题?首先,可以最大限度地减少移动及搬运距离等,增加作业的附加价值;第二,可以实现流线化生产,减少在制品库存,从而缩短生产周期;第三,可以大幅提高工序间的平衡,减少等待浪费,提升生产效率;第四,可以提高空间利用率及单位面积利用率;第五,还可以提升产品品质,改善作业环境。
企业到底应该如何实施精益布局?同样以上述企业的精益布局咨询项目为例,分享如下观点:
首先需要进行精益生产意识的塑造。对公司的各级员工,进行相关的精益生产的教育训练,塑造精益生产的氛围,然后选定以机械加工线为改善试点线,建立改善的信心,在试点线改善完成后进一步在全厂展开推广。
在具体的改善过程中,首先依据客户的需求,计算出节拍时间,再测定每个工序的加工时间及人力时间,根据这些数据的分析结果,考虑生产线的平衡,决定设立三条生产线。每一条生产线所需要的机器设备数量掌握清楚之后,实施精益布局,将机器设备按照产品工艺顺序布置(详见简图<三>),舍弃了改善前的大批量生产方式,将批量的传输方式改为做一个,检查一个,立即传到下一制程的“单件流动”生产方式,以减少工序间的在制品库存,因为剔除了产品在工序间的等待时间,进而使得整个生产周期大幅缩短,此外改变了作业人员的配置方式,舍弃固定的一人一个工序的“单能工”配置方式,而改用以节拍时间为基础来决定人员的配置,并且采用多能工作业方式。
通过改善,使生产周期由改善前的11天缩短至4天,生产效率由原来的每人每天生产150件提升到280件,产品的返修率也从原来的17%下降至7%,厂地面积由改善前的1560平方米缩减至980平方米,改善后有形绩效为:年节省金额102万元RMB;在无形绩效方面,公司的精益生产氛围整体得到提升,物流通道畅通化、透明化,生产现场的异常状况更加容易识别,现场的工作环境也因在制品库存的减少显得更加开阔明亮,井然有序,员工也能发挥互助合作的团队精神。
模型简图<三>
当然一份好的精益布局方案的设计,需要遵循一定技巧及原则,笔者根据多年现场改善及咨询经历总结如下:1. 统一原则:在精益布局设计和改善时,必须将各工序的人、机、料、法、环5要素有机结合起来并保持充分的平衡,因为5要素一旦没有统一协调好,作业容易割裂,增加物料搬运的次数等浪费。
2. 最短距离原则:在精益布局设计与改善时,必须要遵循移动距离,移动时间最小化,因为移动距离越短,物料搬运所浪费的时间和费用就越小。
3. 人流物流畅通原则:在进行精益布局时,必须使工序没有堵塞,物流顺畅无阻。在精益布局时应特别注意:尽量避免倒流交叉现象,否则会导致一系列意想不到的后果,如品质问题、管理难度问题、生产效率问题、安全问题等。
4. 充分利用立体空间原则:随着地价的不断攀升,企业厂房投资也水涨船高,因此如何充分利用立体空间就变得尤其重要,它直接影响到产品直接成本的高低。
5. 灵活机动原则:应尽可能适应变化、随机应变、如面对工序的增减、产能的增减能灵活应对。为了能达成灵活机动原则,在设计时需要将线、电、气与作业台分离、不要连成一体、设备尽量不要落地生根而采取方便移动的装置。
6. 安全满意原则:在进行精益布局设计时,必须确保作业人员的作业即安全又轻松,因为,只有这样才能减轻作业疲劳。请切记:材料的移动、旋转动作等可能会产生安全事故,抬升、卸下货物动作等也可能会产生安全事故,同时也会加剧作业的疲劳度。
精益布局是一个不断改进,不断完善的过程,需要不断执行PDCA改善,切记:“布局是没有最好,只有更好!
企业推动精益布局的过程,不是简单的设备、工装的搬迁,需要各个部门人员的协同合作和支持,这是一个系统工程,特别需要企业高层领导的支持和长远的视野。采用精益布局,也会由于一系列的原因导致产能的波动,我们需要坚定信心,实现我们既定的目标,这样才会在精益之路上走得更远。
作者简介:
王海军,现任深圳市派利企业管理顾问有限公司管理顾问。曾任世界500强富士康科技集团CMMSG事业群IE主管、专案Leader、CMMSG事业群精益变革小组核心成员,在现场管理方面拥有丰富的实战经验,对精益生产有着全面的视野和独到的见解。专长领域:精益生产、现场管理。